Process flow of recycled polyethylene terephthalate (PET)
PET, scientific name: polyethylene terephthalate, is a linear thermoplastic.
PET is usually a crystalline plastic. Due to its advantages of light weight, not easy to break, and low energy consumption, PET bottles have replaced some traditional packaging materials and are widely used in food, beverage, cosmetics and other fields. The recycling and reuse of PET is the process of recycled PET.
The recycling process of PET bottle flakes is to separate the PET bottle body from the cap, label, etc., and then pulverize, clean and dry.
It's specific process is as follows:
(1) The first is the selection process: the selection and classification of various PET bottle flakes. Tear off the trademarks on the outside, most of these trademarks are OPP, and there are also some PVC shrink films, which must be peeled off first.
(2) In the pulverization process, rinse with water during the pulverization process to remove the dirt in various PET bottle flakes.
(3) Put these fragments into the steam treatment device, add flake alkali, and remove the greasy and other stubborn impurities.
(4) Rinse with clean water, dry the remaining water and pack it in bags. Then dry in a vacuum oven.
(5) Spinning, shaping, stretching with hot water steam, and shaping again.These two factors will affect the service life of the plasticizing components of the injection molding machine.
Damage caused by improper workmanship.
(1) Long-term use of high back pressure sol will speed up the wear of the three small plasticized parts. This situation generally occurs when toner is used. Since the toner is difficult to disperse, the method of increasing the back pressure is adopted.
(2) For plastics with high viscosity, fast sol is used for sol, so that the screw produces stress fatigue.
(3) For high temperature plastics, especially plastics with glass fiber added, the high-speed sol method shall not be used.
chemical corrosion
The corroded metal material is an iron component. Common corrosive plastics are: flame retardant plastics, acid plastics, PVC plastics, etc. After the screw, melt barrel and flange are corroded, some pits are formed on the surface, and the surface is rough, which makes the flow resistance of the molten material large when the injection molding machine is working. Some materials tend to adhere to the surface, causing decomposition and carbonization. If the corrosion is severe, the gap between the screw and the melt cylinder will become larger, the leakage flow will increase, and the injection molding efficiency will be reduced.
Whether it is a flame retardant plastic or an acid glue, the acid gas will be decomposed when the plastic is processed at high temperature, and the plastic melt will easily carbonize and stick to the metal. Therefore, on the one hand, the plasticizing components should be made of stainless steel or surface chrome plating; on the other hand, low back pressure, low temperature and low shear processes should be used as far as possible in production and processing to reduce the degradation of plastics;
Thirdly, due to the thermal sensitivity of the above plastics, too high temperature or too long heating time will easily cause plastic decomposition, degradation and carbonization. Therefore, artificial shutdowns should be avoided and reduced in the production process. If it is necessary to shut down, the temperature should be lowered first, the material gate should be closed, and after the molten material in the sol cylinder is finished, the sol cylinder should be cleaned with PP material or PS material before shutdown.
.
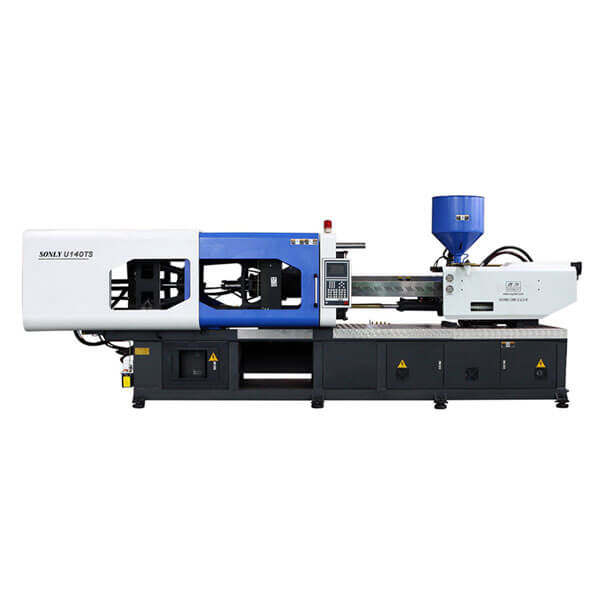