The quality of the hydraulic system of the injection molding machine not only depends on the rationality of the system design and the performance of the system components, but also because of the pollution protection and treatment of the system. The pollution of the system directly affects the reliability of the hydraulic system of the injection molding machine and the use of components.
According to statistics, about 70% of the hydraulic system failures of injection molding machines are caused by pollution. The main hazards of oil pollution to the system are as follows:
1. Contamination and wear of components
Various pollutants in the oil cause various forms of wear of components, and solid particles enter the gap of the moving pair, causing cutting wear or fatigue wear on the surface of the parts. Erosive wear is caused by the impact of the solid particles in the high-velocity liquid flow on the surface of the element. The water in the oil and the products of oxidative deterioration of the oil have a corrosive effect on the components. In addition, air in the oil in the system causes cavitation, causing erosion and damage to component surfaces.
2. Component blockage and clamping failure
Solid particles block the gaps and orifices of hydraulic valves, causing spool blocking and clamping, affecting working performance and even causing serious accidents.
3. Accelerates the deterioration of oil performance
The water and air in the oil are the main conditions for the oxidation of the oil with their thermal energy, and the metal particles in the oil play an important catalytic role in the oxidation of the oil. In addition, the water and suspended bubbles in the oil significantly reduce the motion pair. The strength of the oil film between them reduces the lubricating performance.
system maintenance
A system is generally flushed before it is officially put into operation. The purpose of flushing is to remove contaminants, metal chips, fibrous compounds, iron cores, etc. remaining in the system. During the first two hours of work, even if the system is not completely damaged, it will cause a series of failures. Therefore, the following steps should be followed to clean the oil circuit of the system:
Clean the tank with an easy-drying cleaning solvent, then use filtered air to remove solvent residue.
Clean all the pipes of the system, in some cases, it is necessary to immerse the pipes and joints.
Install an oil filter in the pipeline to protect the oil supply line and pressure line of the valve.
Main Features:
One.The Lock Section
1.Arch template, effectively protects the mould, especially suitable for big template with small mold.
2.The electric ruler is installed on the crosshead, the position is more precise.
3.The front connecting rod uses connected structure, increases the rod strength, and easy for assembly
4.The connected tail-board stills itself with big lock shaft, improves tail-board strength, and ensures zero abrasion of the tail-board, easy for maintenance.
5.Connected movable plate, improves its rigidity and reduces deformation
6.Connected thrust bearing, improves its strength and stills itself with small lock shaft, ensures zero abrasion.
7.Arch template fully complies with mechanical property, largely improves template strength.
8.More reasonable toggle design, speeds and stabilizes mold opening and closing.
9.Adjustable movable plate mounting plate, makes the installation easier.
10.Mixed design of T-shape groove and die hole, increases universality of the mold.
Two.The Injection Section.
1.Bridge type support, improves injection smoothness.
2.Longer length-diameter ratio screw design, improves plasticizing effect.
3.Double seal structure, ensures no oil leakage.
4.Withhold type press plate, easy for debugging and assembly.
5.Bijection structure, improves stability.
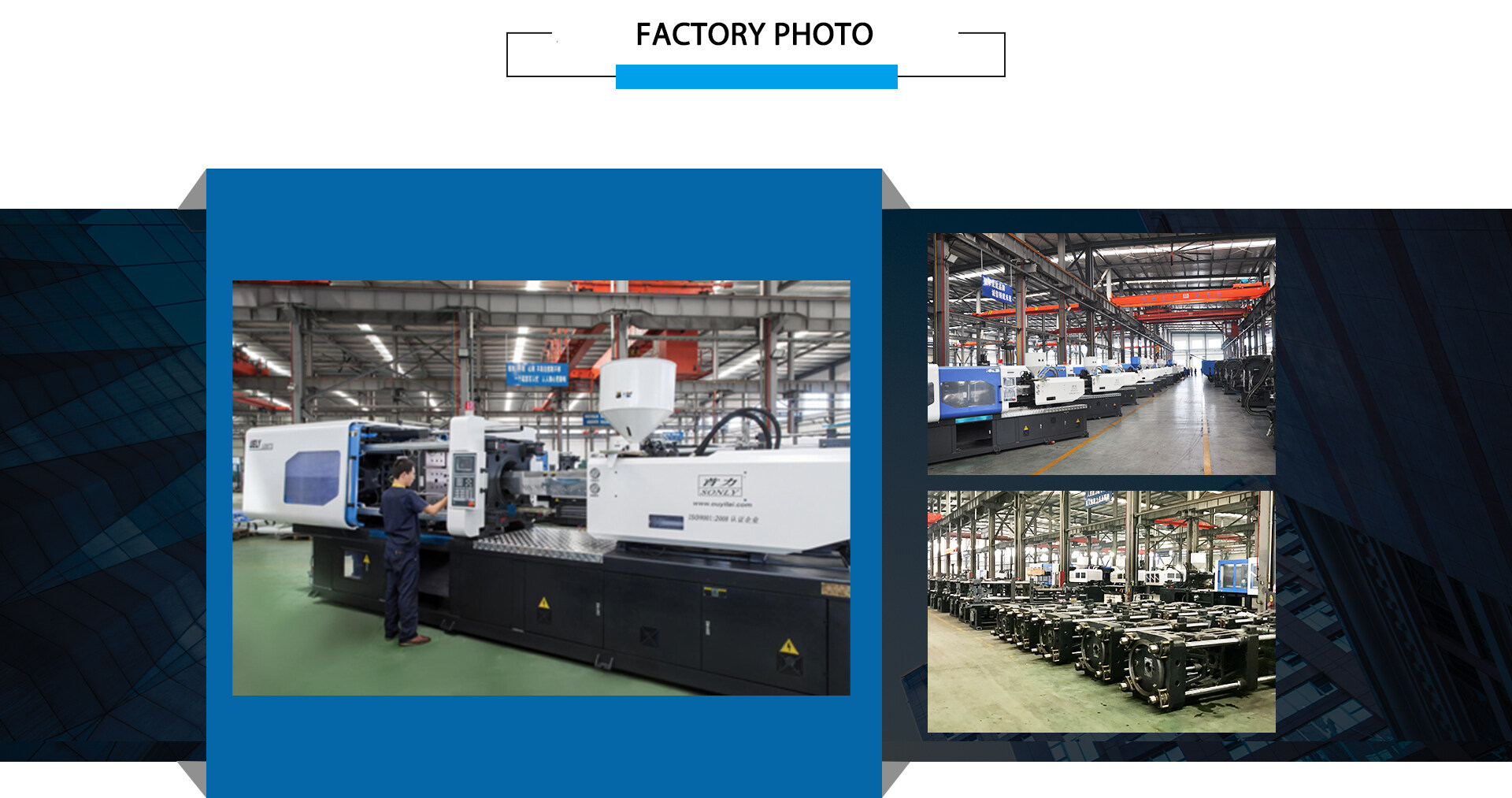
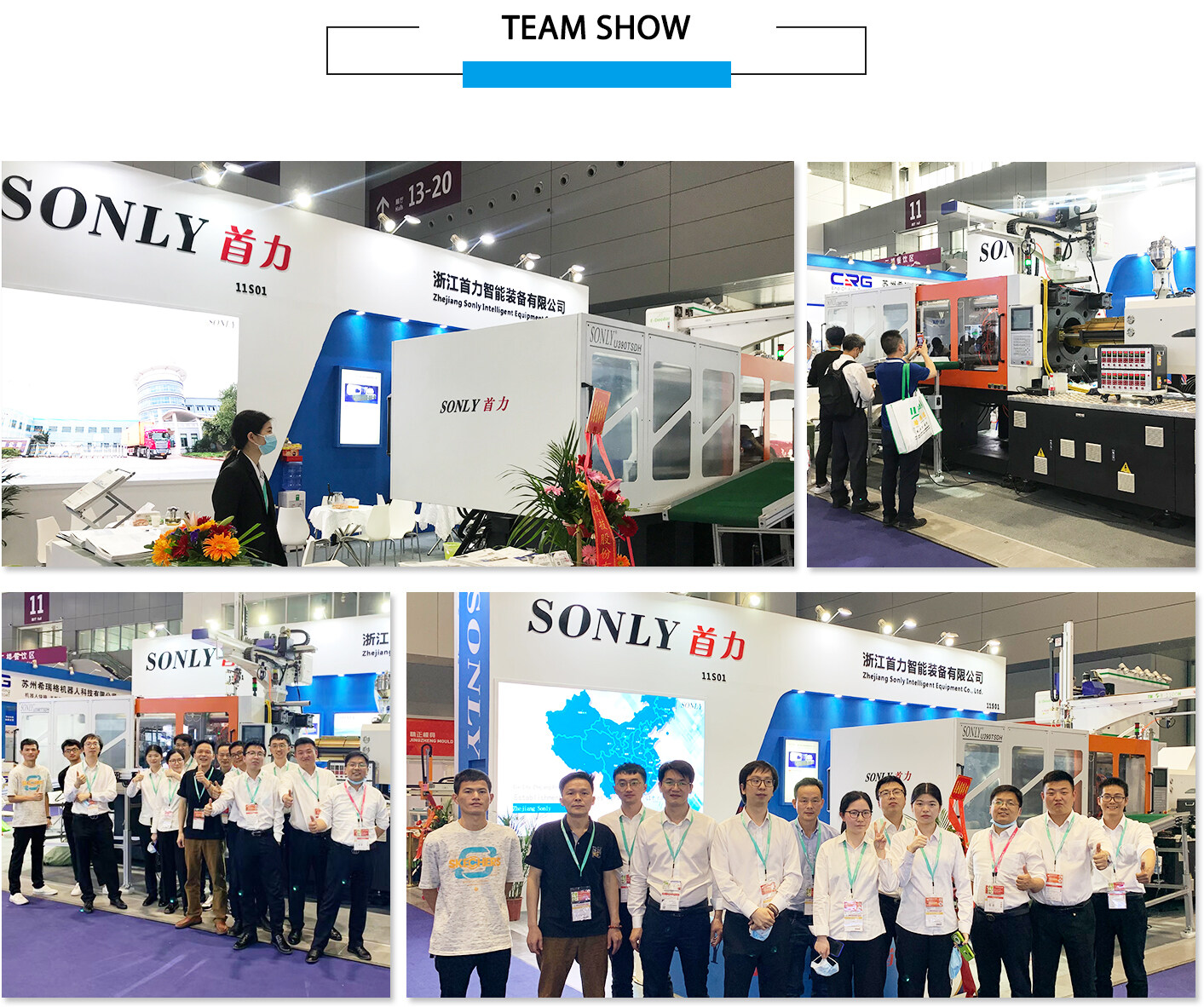
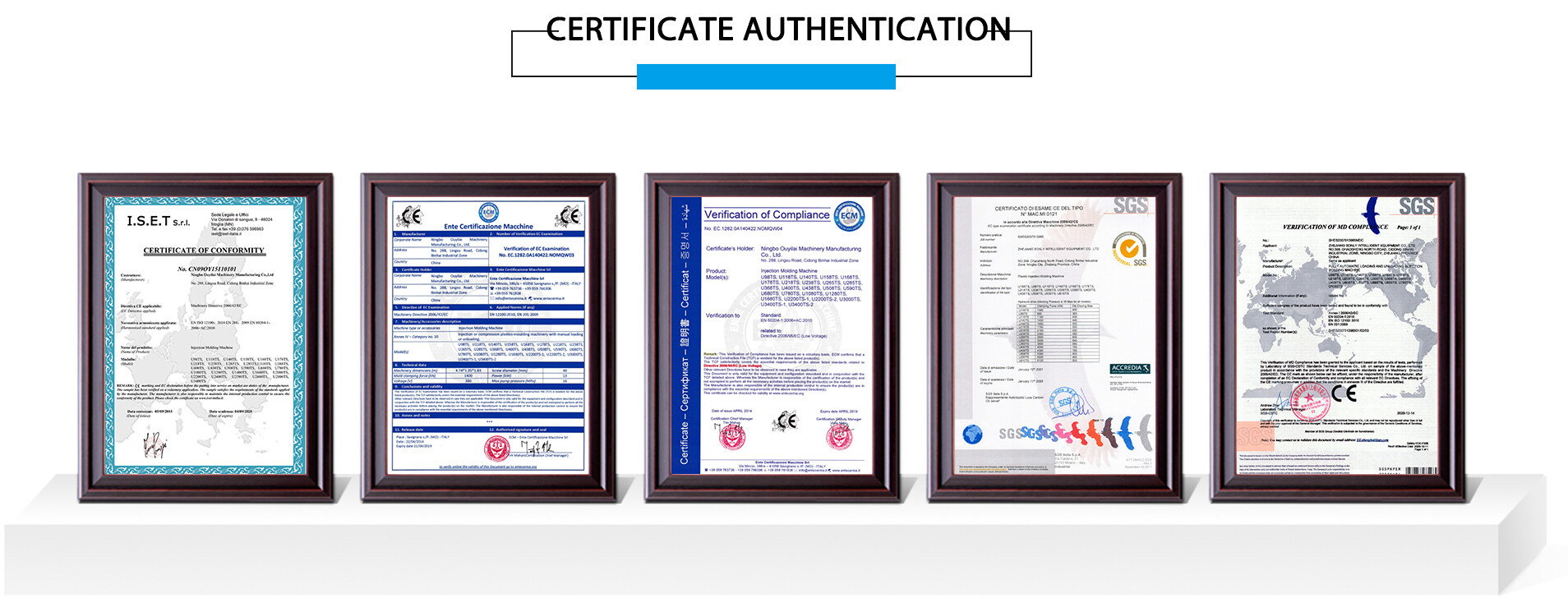
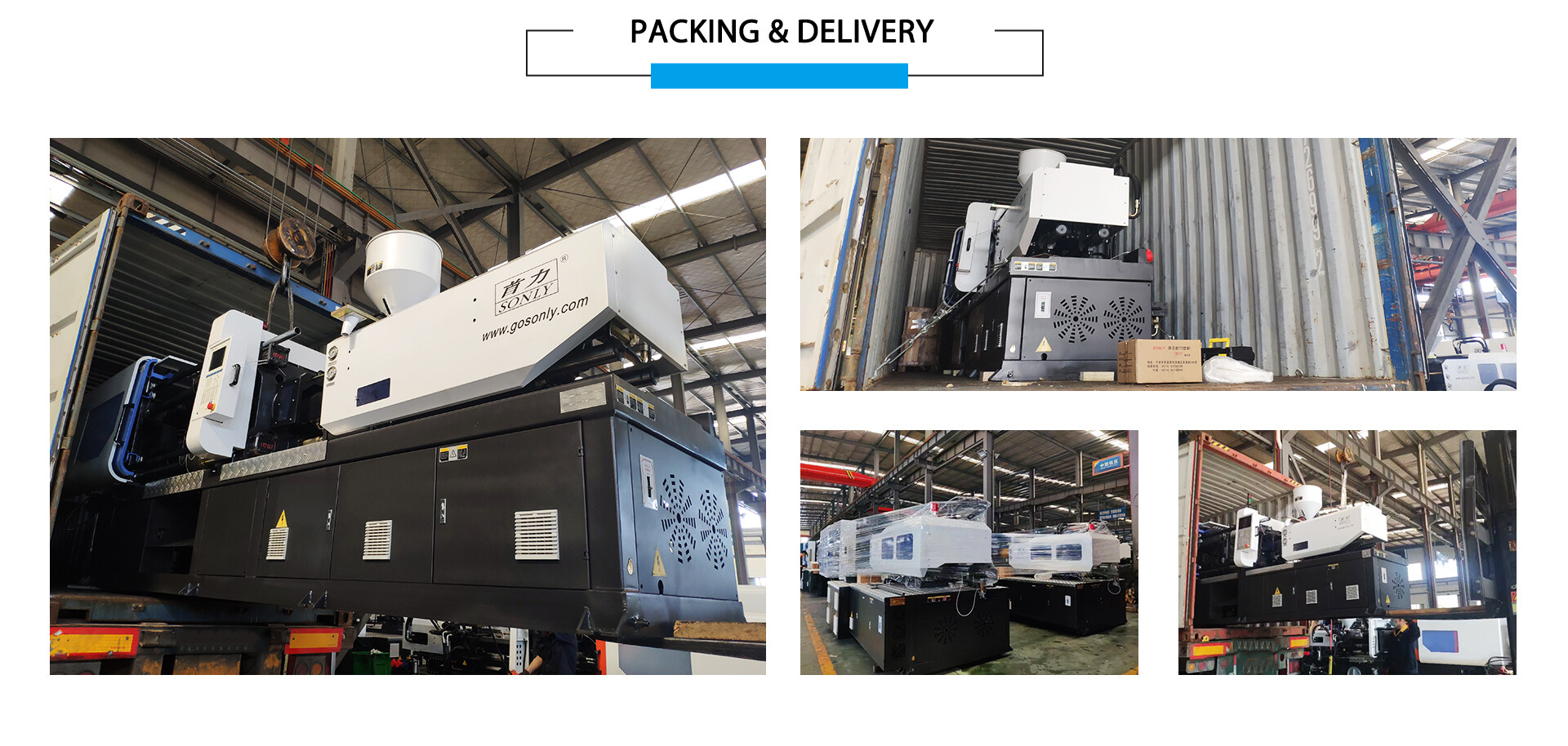